Essential Insights into Inventory Cost Calculators
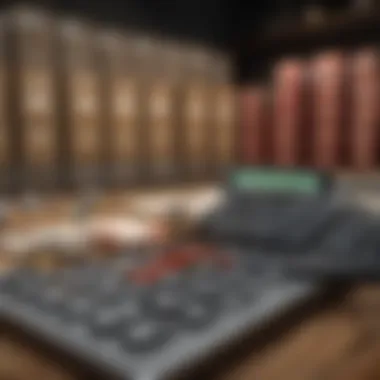
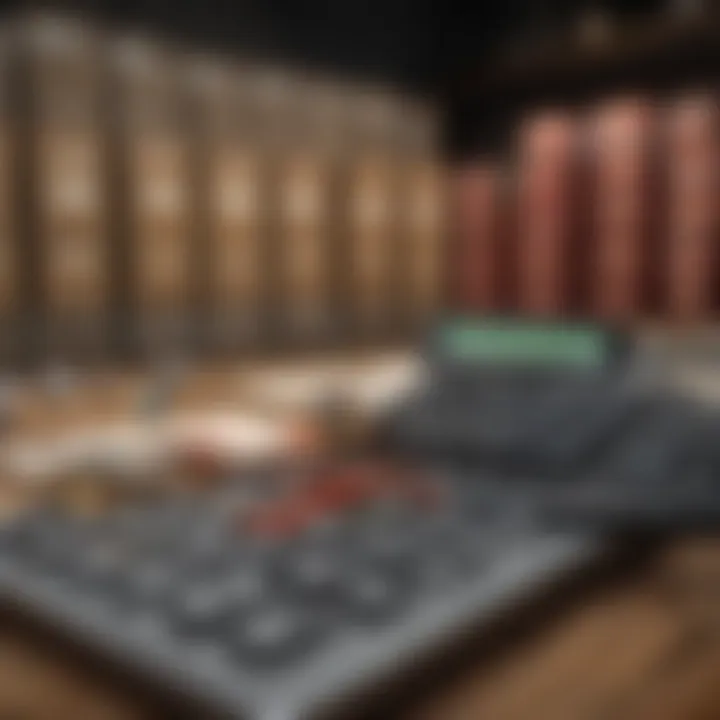
Intro
In today’s business landscape, understanding how to manage inventory costs has never been more essential. Inventory is not merely a collection of goods; it represents capital that is tied up, waiting to find its way to the bottom line. For both budding entrepreneurs and experienced investors, grasping the concept of inventory cost calculators is pivotal in making informed decisions that affect cash flow and overall profitability.
This guide aims to unravel the complexities surrounding inventory cost calculators by dissecting their function, types, and the best practices for their effective use. Not only will we venture into the nitty-gritty of the underlying principles of inventory costing, but we’ll also explore the benefits and limitations these tools offer. Essentially, our goal is to equip you with the insights needed to harness these calculators effectively as part of your financial strategy.
Whether you are a novice trying to grasp basic concepts or a seasoned investor looking to refine your management techniques, understanding inventory costs can provide clarity and enhance your decision-making processes. Let's dive right in!
Prologue to Inventory Cost Calculators
Understanding inventory cost calculators is crucial for any business that handles stock. These tools are not just fancy software; they are the backbone of effective inventory management. When you think about it, knowing how much your inventory truly costs is as essential as knowing how much cash is flowing in and out.
Effective use of inventory calculators can lead to better decision-making and more efficient operations, ultimately impacting your bottom line significantly. Take a moment to consider: When was the last time you felt truly in control of your stock levels? Too often, businesses find themselves overstocked or understocked, causing cash flow issues or missed sales opportunities. That's where these calculators come into play.
Why are Inventory Cost Calculators Important?
- Cost Efficiency: By projecting potential costs associated with maintaining inventory, these tools save businesses from making financial blunders that can lead to significant revenue loss.
- Accuracy in Reporting: A good inventory cost calculator improves reporting accuracy, giving stakeholders a clearer view of financial health. It mitigates the guesswork that often accompanies manual calculations.
- Forecasting Capabilities: They allow businesses to forecast future inventory needs, taking into account variations in demand, seasonal fluctuations, and other market factors.
Considerations When Using Inventory Cost Calculators
While these tools can be lifesavers, they aren't magic bullets. A few key considerations come into play here:
- Data Integrity: The accuracy of inputs is vital; garbage in, garbage out rings true here. Any miscalculation or incorrect data will skew results, leading to poor decisions.
- Understanding Limitations: It's easy to get lost in the features and forget the constraints of the chosen calculator. Knowing when a calculator can be overkill or underwhelming is crucial.
- Continuous Learning: The landscape of inventory management evolves; thus continual learning about best practices and new features can make a huge difference.
Given the heavy lifting that these calculators do, they are definitely worth keeping an eye on. Whether you're just beginning your inventory journey or are a seasoned veteran in finance, recognizing the value of these tools is a key part of optimizing your operational strategies.
"Effective inventory management isn't just about keeping track; it's an ongoing strategy that impacts every facet of your business."
In summary, inventory cost calculators are not merely tools; they’re essential for navigating the complexities of stock management. By leveraging these calculators effectively, businesses can streamline operations, make informed decisions, and ultimately pave the way for sustained growth.
Understanding Inventory Management
Managing inventory is often overlooked but is crucial in keeping a business running smoothly and profitably. From those small retail shops to vast manufacturing plants, every organization needs to keep an eye on their inventory levels. Understanding how to manage inventory effectively can help in minimizing costs, meeting customer demand, and ultimately boosting profits.
Definition and Importance
Inventory management refers to the process of overseeing and controlling the ordering, storage, and use of components that a company uses in the production of the items it sells. This includes managing raw materials, work-in-progress items, and finished goods. Why is it so important? It is like having a roadmap in a foggy terrain. You might know where you want to go, but without clarity on what lies ahead, you may easily get lost.
Good inventory management helps a business to maintain the right amount of stock at the right time. If you have too much inventory, you might face increased storage costs, spoilage, or obsolescence. On the flip side, having too little can lead to missed sales opportunities and disgruntled customers. So, finding that sweet spot benefits a company tremendously.
Key Concepts in Inventory Management
Inventory management encompasses several key concepts that form the backbone of effective stock control. These include:
Stock Keeping Units (SKUs)
Stock Keeping Units, or SKUs, play a crucial role in inventory management. An SKU is a unique identifier for each distinct product and service that can be purchased. What makes SKUs significant is that they allow businesses to track inventory systematically, making it simpler to know what products are in stock, what needs to be reordered, and how fast inventory moves.
One key characteristic of SKUs is their ability to categorize products based on variation, like size, color, or brand. This is super helpful! For example, a t-shirt company may have SKUs for each color and size combination. The primary advantage of using SKUs is the detailed tracking of inventory, but there can be a downside as well. Overcomplicating the SKU system with too many distinct items might lead to confusion or errors in stock management.
Just-In-Time Inventory
Just-In-Time (JIT) inventory is another pillar of successful inventory management. This method focuses on reducing waste and ensuring products are received only as they are needed in the production process. The key feature of JIT is its focus on timing. By having materials arrive precisely when required, companies can reduce storage costs.
The benefits of JIT are quite appealing. Companies can improve cash flow and minimize excess stock; however, there are risks involved. Any disruption in the supply chain can lead to production halts, potentially harming customer satisfaction. Thus, it requires a finely tuned system to benefit from JIT.
Lead Time Optimization
Lead time optimization is about increasing efficiency from when an order is placed to when it is fulfilled. Adjusting lead times can result in significant time savings and improved customer satisfaction. The beauty of this approach lies in its ability to boost responsiveness to market demands.
One of the main characteristics of lead time optimization is its emphasis on planning and forecasting. A business that can predict demand accurately will be better positioned to optimize its lead times. The upside is clear; less waiting time for customers can translate to more sales. However, underestimating a demand surge can lead to product shortages and disappointed customers, which underscores the need for a robust inventory management system.
Understanding these concepts allows businesses to navigate the complexities of inventory management and develop strategies that suit their unique operational needs.
Types of Inventory Cost Calculators
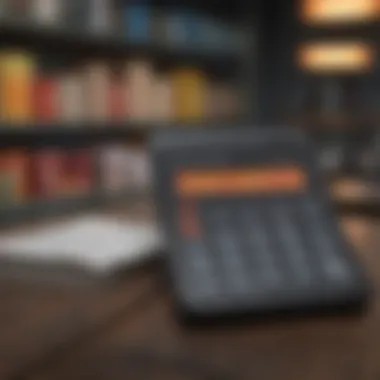
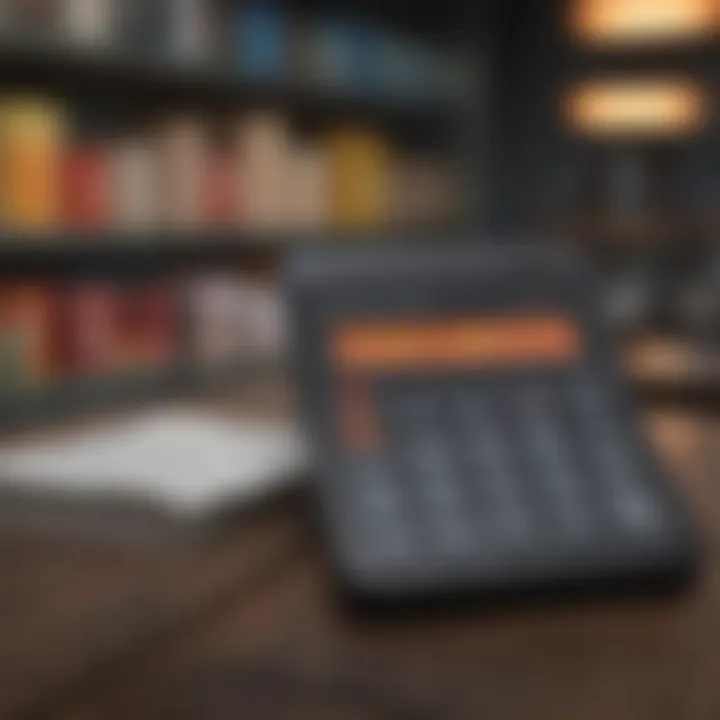
In the world of inventory management, the calculators available serve as crucial instruments for business efficiency. Understanding the different types is essential, because each has unique attributes and functionalities that can greatly influence decision-making. By selecting the right type of calculator, businesses can not only streamline operations but also enhance their financial acuity and strategy.
Basic Inventory Cost Calculators
Basic inventory cost calculators are quite straightforward tools designed for small to medium enterprises looking to keep things simple. These calculators typically require minimal inputs, such as the cost of goods sold (COGS), average inventory, and sales revenue. Their primary goal is to offer a quick calculation of the inventory costs, often focusing on metrics such as inventory turnover rates or basic valuation methods like FIFO (First-In, First-Out).
The beauty of basic calculators lies in their ease of use. They often come in spreadsheet format or as simple online tools that can be accessed anywhere. This accessibility makes them ideal for businesses with limited budgets or those that are just getting off the ground. Moreover, they allow for quick adjustments and on-the-fly calculations, which are invaluable for small business owners who might not have the time or resources for complex software training.
Nevertheless, these basic calculators do have their limitations. Relying solely on them can lead to oversimplified financial insights, which might result in missed opportunities or inaccurate projections. While they’re beneficial for initial undertakings, once a business begins scaling its operations, a move to more advanced tools is often necessary.
Advanced Inventory Management Software
On the other end of the spectrum, we have advanced inventory management software, which is tailored for larger enterprises or those with complex inventory systems. These suites often integrate a variety of features, including tracking multiple categories of inventory, forecasting capabilities, and analytics tools designed to provide comprehensive insights.
Cloud-Based Solutions
Cloud-based solutions stand out in the realm of advanced software. Using a simple internet connection, businesses can access their inventory data from anywhere, which offers immense flexibility, especially for companies with several locations or remote employees. The primary characteristic that makes cloud-based solutions so attractive is their scalability. As a business grows, additional features can be added without the need for a complete overhaul of the system.
Moreover, these systems often come equipped with real-time data analytics. Users can see their stock levels, order statuses, and financial performance in real time, which is a significant advantage in fast-paced markets. However, while they provide flexibility and ease of access, issues surrounding data security and reliance on internet connectivity must be considered as potential drawbacks.
Integration with ERP Systems
Integration with ERP systems represents another pivotal aspect of advanced inventory management tools. Many businesses use Enterprise Resource Planning (ERP) software to coordinate various functions such as finance, HR, and supply chain management. Integrating inventory calculators with ERP systems allows for a seamless flow of information across departments, which enhances efficiency significantly.
This integration allows for automatic updating of inventory levels and cost data across all business facets. It reduces manual entry errors and provides a holistic view of the business’s performance, which is added insight that basic calculators cannot provide. However, the complexity of these systems requires user training, and the initial setup can be resource-intensive.
"Choosing the right inventory calculator can make or break a business's operational effectiveness, highlighting the importance of understanding the tools available."
In summary, the choice between basic and advanced inventory cost calculators should be influenced by the specific needs of a business. While small enterprises might benefit from basic tools, larger operations often require the sophistication offered by advanced solutions. Each type brings its own advantages and disadvantages, and the right fit hinges on the company's scale and operational complexity.
How Inventory Cost Calculators Work
Understanding how inventory cost calculators function is crucial for any business owner or investor looking to optimize their inventory management processes. These calculators serve as an essential tool for breaking down complex financial data into actionable insights, making inventory management less daunting.
Core Functionality
At their heart, inventory cost calculators are designed to evaluate the costs associated with managing stock, and their functionality revolves around several metrics. The primary purpose is to aid businesses in decision-making regarding purchasing, stocking, and pricing strategies. By providing a clear picture of costs, these calculators help businesses identify opportunities for efficiency and profitability.
Moreover, the efficiency of these calculators lies in their ability to handle vast amounts of data and present it in an understandable format. Functions include:
- Cost Analysis: They break down the costs associated with goods sold, storing inventory, and potential loss due to overstock or stockouts.
- Visual Reporting: Many tools feature dashboards that allow users to visualize metrics, trends, and forecasts.
- Scenario Modeling: Users can simulate different inventory scenarios to see potential financial impacts before making commitments.
In short, when utilized properly, these calculators can provide a roadmap to better financial health in managing inventory.
Data Inputs Required
To harness the power of inventory cost calculators, certain data inputs are needed to ensure accuracy. Understanding these inputs can significantly enhance the decision-making process and ensure reliable outputs. Here are the primary data points:
Cost of Goods Sold (COGS)
The Cost of Goods Sold (COGS) is a critical input that refers to the direct costs attributable to the production of the goods sold by a company. This metric includes costs of materials and labor directly tied to product creation. Having a precise figure for COGS is vital; inaccuracies here can distort profitability analysis drastically.
- Key characteristic: COGS helps businesses determine the gross margin and overall profitability.
- Why it matters: It is a foundational element of financial statements, particularly for those seeking to optimize pricing strategies or minimize expenses.
- Unique features: COGS can differ vastly depending on accounting methods—LIFO (Last In, First Out), FIFO (First In, First Out), or weighted average cost—which can affect reported profits.
Inventory Levels
Inventory Levels refer to the quantity of goods that a company has in stock at any given time. This input is crucial because it informs how much capital is tied up in unsold goods, which can affect liquidity.
- Key characteristic: Maintaining ideal inventory levels can reduce carrying costs while ensuring stock availability.
- Significance: It is often necessary for making informed decisions on purchasing, production schedules, and sales forecasting.
- Unique features: Seasonal fluctuations, market trends, and consumer demand can complicate maintaining optimal inventory levels; thus, using historical data to predict future levels is wise.
Price per Unit
The Price per Unit is simply the amount regained from selling each item in inventory. This is a significant aspect, as it directly influences revenue and profit margins.
- Key characteristic: Pricing strategies can make or break a business; finding the right price point is fundamental.
- Importance: Understanding price per unit relative to costs can help businesses strategize how to offer competitive pricing without sacrificing profitability.
- Unique features: Adjusting the price per unit in response to market conditions enables companies to remain agile and profitable. However, price alterations need careful consideration, as they can impact customer perceptions and sales volume.
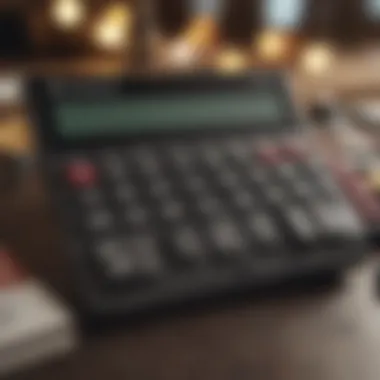
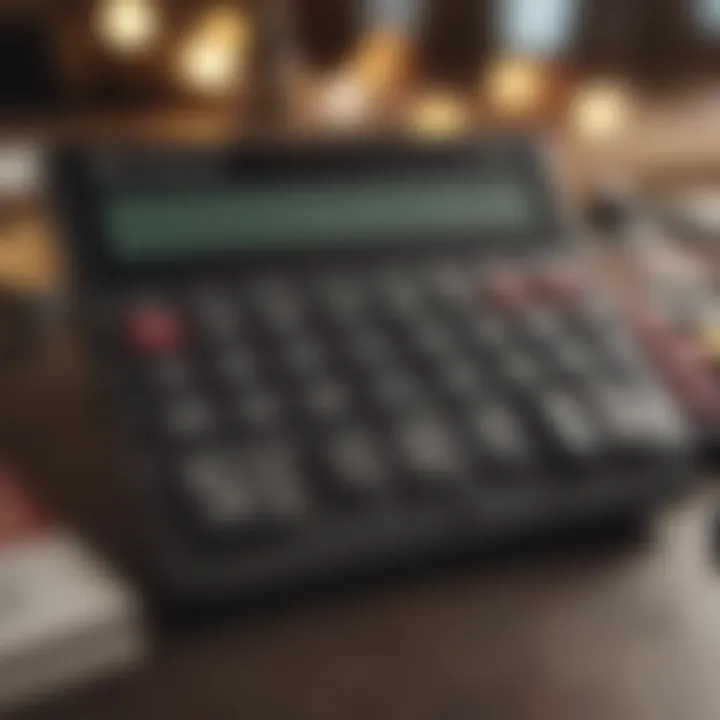
Overall, understanding how inventory cost calculators work empowers business owners and investors alike to streamline inventory processes and make better financial decisions. By mastering the core functionality and essential data inputs, they improve their strategic planning and operational efficiency.
"Effective inventory management is not just about stock levels; it's about understanding the financial implications of every unit in your inventory."
With a grasp of these elements in hand, users can dive deeper into the world of inventory management and truly leverage the tools at their disposal.
Benefits of Using Inventory Cost Calculators
When delving into the complex realm of inventory management, understanding how to effectively use inventory cost calculators can be a game changer, whether you're a fresh entrepreneur or a seasoned investor. These tools are tailored to not just streamline your inventory processes, but to offer several key benefits that significantly enhance the efficiency and effectiveness of decision-making.
Enhanced Decision-Making
A significant advantage of using inventory cost calculators lies in their ability to foster improved decision-making. By providing accurate calculations, these tools help eliminate guesswork. Investors can make informed choices about purchasing inventory, managing stock levels, and forecasting future needs. Imagine you’re at the crossroads of either utilizing funds on excess inventory or reinvesting in new projects. An inventory cost calculator can shed light on potential returns and help prioritize your investments more acutely.
Furthermore, calculators often utilize a variety of metrics to provide a comprehensive picture of inventory costs. Key performance indicators (KPIs), such as turnover rates and carrying costs, become clear and concise, allowing for strategic adjustments to your inventory practices. Consequently, executives can pivot their strategies in real time, maximizing profit margins while minimizing waste.
"Accurate data simplifies complexity in decision-making; without it, you’re sailing a ship in the fog."
Time Efficiency
Time is of the essence, especially in today’s fast-paced business environment. Inventory cost calculators automate tedious calculations and replace manual data entry with streamlined solutions. This automation not only conserves valuable hours but also teams can focus their effort on more crucial aspects of an operation, such as market analysis or strategic planning.
Using these calculators effectively reduces the chances of human error. The fewer the mistakes, the quicker you can get back to business—ensuring that critical decisions are based on solid data rather than guesswork. In fact, organizations report spending up to 50% less time on inventory management tasks when using these calculators compared to traditional methods.
Improved Financial Accuracy
Financial accuracy cannot be overstated when it comes to managing inventory costs. Incorrect calculations can wreak havoc on financial statements, affecting bottom lines and stakeholder trust. Inventory cost calculators facilitate precise computations by aggregating various cost elements—like purchase price, shipping costs, and holding costs—into one coherent figure.
In addition, these tools often offer historical data analysis, enabling businesses to track trends over time. This historical insight leads to a clearer understanding of cost patterns and prepares businesses for seasonal fluctuations. Ultimately, accurate financial reporting can better inform strategic growth plans.
Using inventory cost calculators ensures that your financial data reflects the true state of your inventory, helping organizations make better projections and avoid costly surprises down the line.
Common Limitations of Inventory Cost Calculators
While inventory cost calculators can be invaluable tools for managing stock and finances, they are not without their shortcomings. Understanding these limitations is crucial for both beginners and seasoned investors in developing a realistic expectation of what these calculators can achieve.
Dependence on Accurate Data
Inventory cost calculators thrive on precision, necessitating accurate input data to generate reliable outcomes. If the underlying figures, like cost of goods sold or stock levels, are flawed or miscalculated, the results can be misleading. For instance, if an investor inputs inflated costs or overlooks certain expenses, the tool might signal an unhealthy profit margin or suggest excessive stock levels. Thus, it's vital for businesses to establish a consistent data collection process. Without that, any reliance on the calculator becomes a bit like sailing a ship without a compass—likely to lead to disaster.
Potential Overhead Costs
An often-overlooked pitfall involves the overhead costs associated with maintaining these calculators. Whether using advanced software or basic models, businesses face potential fees and training requirements that may not be immediately evident. This includes subscription costs for cloud solutions or updates for desktop software. For smaller operations, these overheads can add up quickly, eating into the very profits the inventory calculator is supposed to help optimize. Therefore, it's essential to perform a cost-benefit analysis before implementing any new tool.
User Misinterpretation of Results
A third crucial limitation pertains to the potential for users to misinterpret the results generated by the calculators. An investor simply glancing at figures may draw incorrect conclusions without delving deeper into the data's implications. For example, if a calculator suggests a low inventory turnover rate, the user might hastily decide to cut back on orders, unaware that seasonal fluctuations in demand could be at play. This misreading can occur especially in a fast-paced market where nuances are easily overlooked. Educating users on how to interpret these results properly can help counteract this issue.
"An informed decision is always better than a rushed one."
By understanding these limitations, investors can navigate the pitfalls more efficiently and leverage inventory cost calculators for greater financial insight. Emphasizing accurate data, recognizing potential overhead, and comprehensively understanding the results will enhance the effectiveness of these valuable tools.
Best Practices for Utilizing Inventory Cost Calculators
Utilizing inventory cost calculators can certainly streamline the inventory management process significantly. Just like any tool, understanding how to use it effectively can make all the difference. Implementing best practices not only maximizes the accuracy of calculations but also enhances decision-making and allows businesses to adapt more fluidly to changing market conditions.
Adopting these best practices involves several areas of focus. From setting a routine for updates to providing appropriate training for employees, diligence in these aspects links directly to improved organizational efficiency and a higher bottom line.
Regular Updates and Maintenance
It’s easy to overlook the nitty-gritty details of keeping inventory cost calculators current, but doing so is essential. Outdated information can lead to miscalculations and ineffective strategies. Think of it as maintaining a car; if you don’t change the oil, eventually, the engine won’t run smoothly.
Key Points:
- Schedule Regular Check-ups: Designate specific times (monthly, quarterly, or bi-annually) to review and update your data inputs. Changes in supplier prices, production costs, or sales prices must be reflected to maintain accuracy.
- Monitor Software Updates: If using advanced inventory management software, it’s crucial to stay informed about any updates or new features that could enhance your calculator's functionality. Consider visiting the software provider's website for announcements.
- Backup Data Frequently: Regularly back up your inventory data. In case of system failures or data corruption, you wouldn’t want to lose valuable information. Scheduled backups can provide peace of mind.
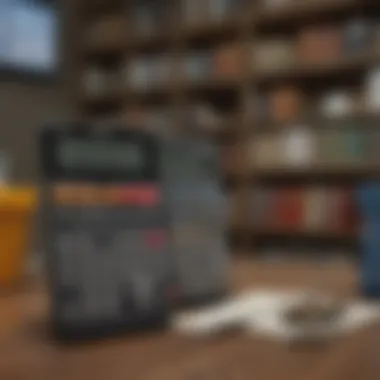
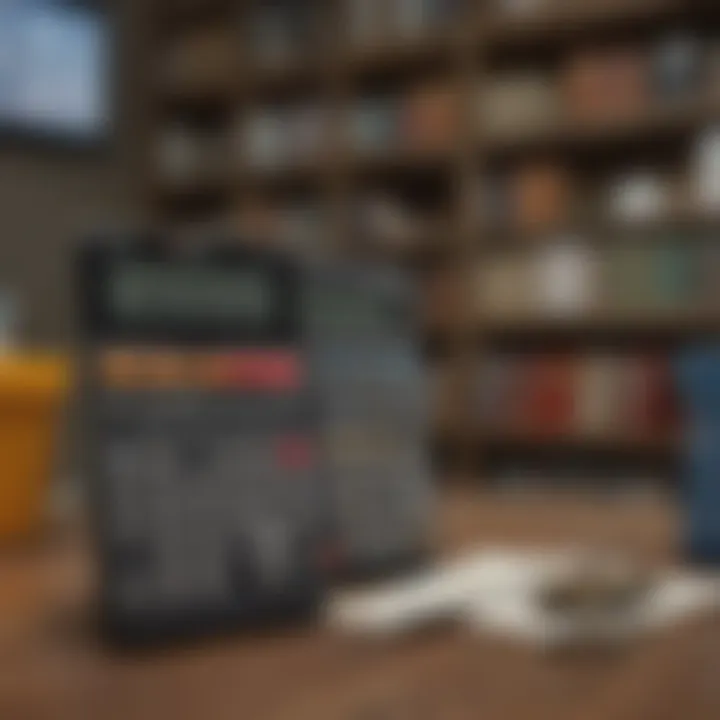
Improving the routine around maintenance serves a dual purpose; it supports the integrity of your financial data while also building a culture of responsibility within your team.
Training Employees on Usage
Even the best tool is only as good as the hand that wields it. Training employees on how to effectively use inventory cost calculators not only increases efficiency but also empowers them to make informed decisions based on accurate data. Imagine trying to bake a complex recipe like a soufflé without understanding the oven settings. The results could leave a lot to be desired!
Considerations for Training:
- Workshops and Practical Sessions: Instead of a one-time seminar, consider ongoing training sessions where employees can practice using the calculators with real inventory data. This approach not only improves familiarity but also boosts confidence among the team.
- Documentation and Resources: Provide easy access to user manuals and online resources. Having a reference guide at hand makes it easier for employees to troubleshoot minor issues independently without halting productivity.
- Encourage Feedback: Create a system where employees can share their experiences using the calculators. They might encounter challenges that need addressing or even discover tips that could be beneficial for the team.
By investing in training, employers send a clear message: they value their employees' skills and are committed to enabling them to harness the full power of inventory management tools.
"Training is an investment, not an expense."
Case Studies: Successful Implementation
Implementing inventory cost calculators can be a game changer for many businesses. Case studies provide real-world examples that illustrate the benefits and considerations involved in using these tools effectively. By examining how different sectors have integrated these calculators into their operations, valuable insights emerge that can guide others in similar endeavors. Success stories showcase not only the tools’ functionalities but also their adaptability in various contexts.
Retail Sector
In the retail industry, accurate inventory management is crucial. A prominent clothing retailer, for instance, managed to streamline its operations by incorporating an advanced inventory cost calculator. Initially plagued by overstocking issues, leading to cash flow problems, the company adopted a cloud-based solution that enhanced real-time data insights.
The calculator allowed the retailer to assess inventory levels and track sales in real time. As a result, it could maintain optimal stock levels, reducing costs associated with unsold merchandise. After implementing this system, the retailer reported a remarkable 30% reduction in carrying costs within just six months of use.
This change did not only help with cost efficiency but also improved the freshness of the stock, keeping the product offerings aligned with current trends.
Furthermore, employee training on the new system played a key role in its success. Staff became adept at using the calculator, which led to better inventory decisions and ultimately boosted sales.
Manufacturing Sector
In the realm of manufacturing, where the production schedules depend heavily on stock availability, a well-defined approach to inventory calculation is vital. A medium-sized electronics manufacturer faced challenges in its supply chain management, often leading to delays in production due to incorrect inventory assessments. By integrating an inventory cost calculator, the firm was able to completely transform its operation.
The transition involved setting up a sophisticated calculator that incorporated cost of goods sold, production lead times, and component availability. As a result, the manufacturer achieved a 25% increase in production efficiency. The enhanced visibility into inventory costs allowed the company to identify bottlenecks and minimize wastage.
Moreover, the use of this tool facilitated strategic sourcing decisions, allowing the manufacturer to negotiate better terms with suppliers based on precise inventory needs. The overall benefits included not just improved cash flow but also the ability to expand product lines based on accurate demand forecasting.
Just like in retail, training and active employee involvement were pivotal for a smooth transition. Regular workshops and feedback sessions allowed employees to adjust to the new systems, ensuring that potential challenges were addressed promptly.
"The integration of inventory cost calculators was not just a technical upgrade; it became a cornerstone of our operational strategy." - Manufacturing Sector CFO
Future Trends in Inventory Management
The landscape of inventory management continues to evolve at a rapid pace, driven by advancements in technologies and changing market demands. Understanding the future trends in this area is crucial for both novice and seasoned investors aiming to leverage inventory cost calculators effectively. These trends bring numerous benefits, including better visibility, enhanced decision-making capabilities, and improved efficiency in operations.
Artificial Intelligence and Automation
Artificial intelligence (AI) is reshaping inventory management practices. With AI algorithms, businesses can analyze vast amounts of data quickly, identifying patterns and trends that human analysis might miss. Here are some specific areas where AI and automation are making a difference:
- Demand Forecasting: AI can predict future inventory needs based on historical data, seasonality, and market trends. This helps companies avoid stockouts or overstock situations.
- Inventory Optimization: Algorithms can automatically adjust stock levels and reorder points, ensuring that the right amount of inventory is always on hand, reducing waste and improving cash flow.
- Automated Reporting: With advanced automation tools, generating performance reports becomes a breeze. This allows managers to focus more on strategy rather than data compilation.
Using AI in inventory management isn't just a fleeting trend; it’s becoming a necessity. Companies that embrace these technologies often gain a competitive edge, effectively streamlining operations and offering better service to customers.
Blockchain for Inventory Transparency
Blockchain technology is not just buzzing in the tech streets for cryptocurrencies. It is making a notable impact in inventory management too. The transparency that blockchain offers can significantly enhance trust and efficiency within supply chains. Here are several key benefits of using blockchain for inventory management:
- Traceability: With blockchain, every transaction is recorded in a secure and unchangeable ledger. This means businesses can trace the origin of their products, verifying authenticity and reducing chances of fraud.
- Real-time Visibility: Blockchain provides an up-to-the-minute view of inventory levels across the supply chain, allowing managers to make informed decisions faster and adjust operations accordingly.
- Smart Contracts: These are self-executing contracts with the terms directly written into code. They can automate various processes in the supply chain, ensuring compliance and reducing operational costs.
In a nutshell, these future trends are more than just buzzwords. Efficiency, transparency, and a data-driven approach are becoming the hallmarks of successful inventory management strategies. Failing to adapt could leave businesses trailing behind competitive players who utilize these innovations effectively.
"Embracing technology in inventory management isn’t just about keeping up; it’s about setting the pace."
As organizations navigate these complexities, they remodel their strategies accordingly, setting themselves up for success in a fast-paced economic environment.
Closure
In wrapping things up, the importance of this article resides in how it underscores the multifaceted role inventory cost calculators play in the broader landscape of inventory management. These tools are more than just calculators; they are vital checkpoints for businesses aiming to fine-tune their operational efficiency and financial accuracy.
First, it’s essential to appreciate the benefits these calculators bring. They streamline decision-making, allowing both novices and experts to navigate the complexities of inventory management with greater ease. With accurate data inputs, businesses can swiftly assess their inventory health, leading to informed stock purchases, optimized storage solutions, and ultimately, enhanced profitability.
Moreover, the considerations around using these calculators cannot be overlooked. Relying solely on automated tools without understanding the underlying data may result in miscalculations. Thus, a continuous education process for employees, along with regular updates to the systems in place, is critical for success. Best practices, as detailed in earlier sections, ensure that the tools are not just utilized but are leveraged to their maximum potential.
Through exploring the trends in inventory management, one can envisage the contours of a changing landscape. Innovations like artificial intelligence and blockchain technology aren't merely concepts for the future; they are here, reshaping the way inventory is managed. Adapting to these trends can provide businesses with a competitive advantage.
An often overlooked aspect is maintaining a mindset of adaptability. As the market evolves, so should the strategies surrounding inventory management. Embracing new technologies and methodologies equips businesses not only to survive but to thrive.
Investing time and resources in understanding and implementing inventory cost calculators can lead to transformative outcomes for any business.